Welcome
Take a peek inside our facilities. We have over 50,000 square feet of production space located in Western New York.
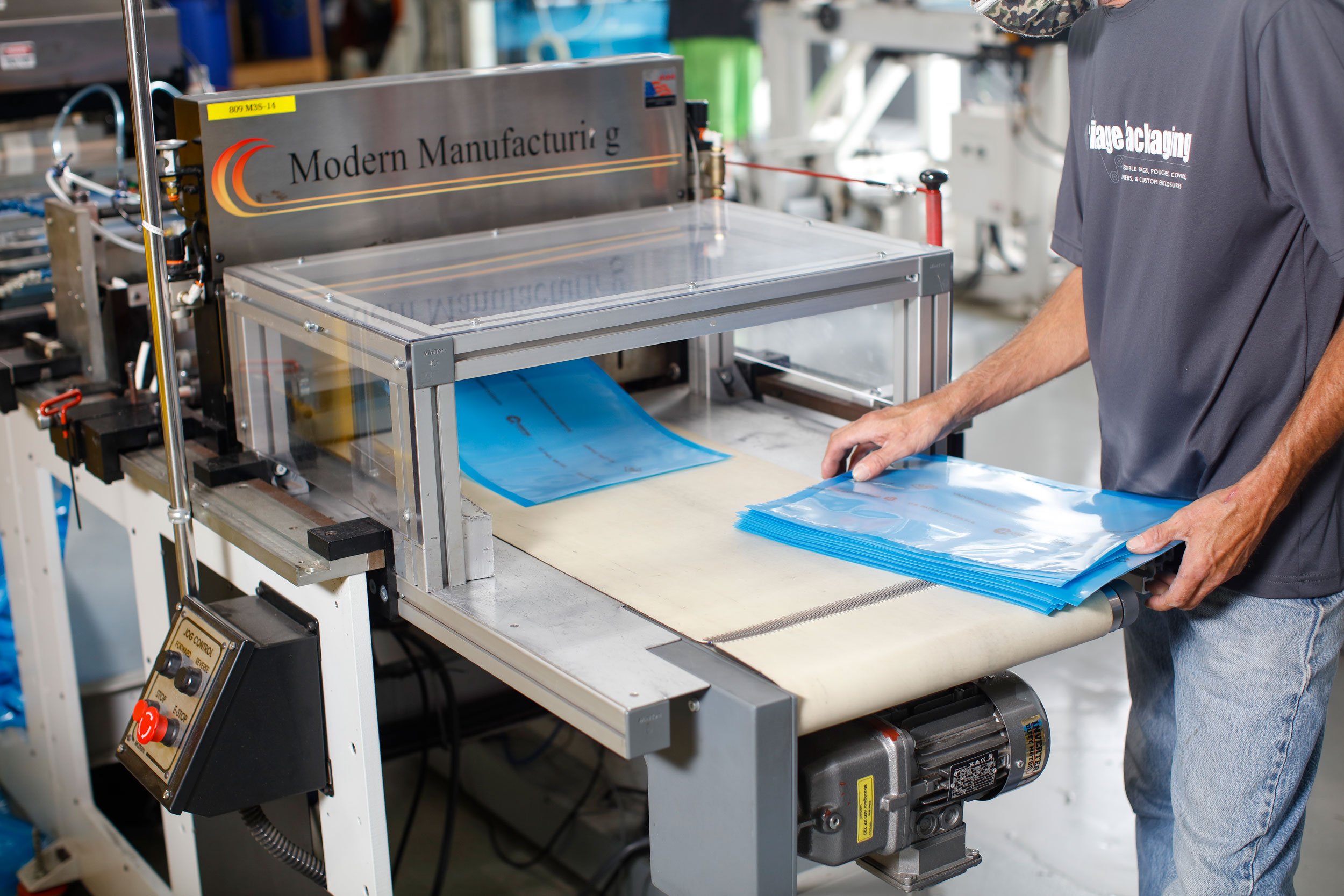
Automated Production
Frequently Made Products
Bottom gusset stand-up pouches with molded fitments for food products.
2 seal faraday shielding bags
Flat and bottom gusset pouches
for molded labware.Stand-up pouches with molded fitments for auto body paste.
Stand-up pouches with zip closures and tear notches for powdered product.
…and many more!
Our Machines
14” Automatic Pouch Machine
Makes flat 2 or 3 seal pouches and continuous barrier tubing.
24” Stand Up Pouch Machine
Makes stand up pouches, flat pouches, side gusset bags, and barrier tubing.
36” Pouch Machine
Makes stand up pouches; inserted-web, side gusset pouches, and flat pouches. This machine has additional contour-sealing and die-cutting capabilities.
46” Automatic Pouch Machine
Capable of high speed flat pouch production.
72” 4-Web Automatic Pouch & Liner Machine
Produces side gusset bags that can be taper-sealed and formed into glove fit container liners, and it can make large flat bags or blankets.
Contour-Sealing Platen & Die Cut Machine
Has automatic in-line flanged fitment installation along with the ability to make shaped seals and shaped pouch configurations.
Imprinting
Our inkjet printers print 1-color text, barcodes, Julian dates, and lot numbers directly onto pouches.
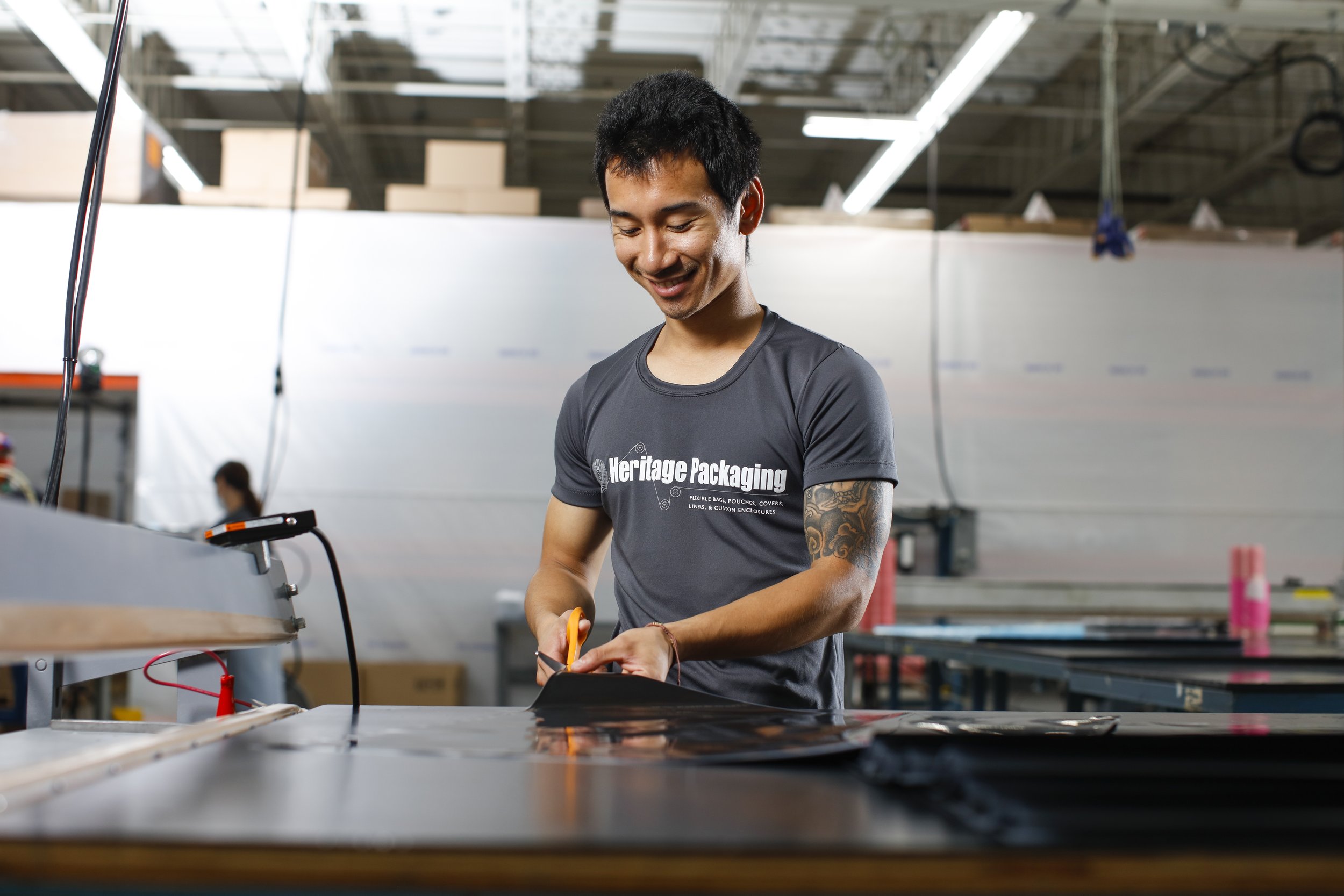
Hand Fabrication
Made by Hand
Some products are too sophisticated to run on automatic machinery and require hand fabrication by our specially trained employees. Our fabricators are skilled at manipulating flexible materials in ways that machines simply cannot.
This area of the plant is used to make two and three-dimensional, custom-shaped, flexible products like covers, liners, and bags; and allows us to work on prototyping for items that will eventually run on automatic machines.
Frequently Made Products
Intake and exhaust covers for cargo planes.
Large 3-D, anticorrosion covers for gas turbines shipped overseas.
3-D carton Liners for automotive parts.
Insulated air conditioning ducts for the aerospace industry.
…and many more!
Our Equipment & Machinery
Straight line heat sealers
Contour sealing equipment
Die-cutting machines
Sheeting machines
Grommeting machine
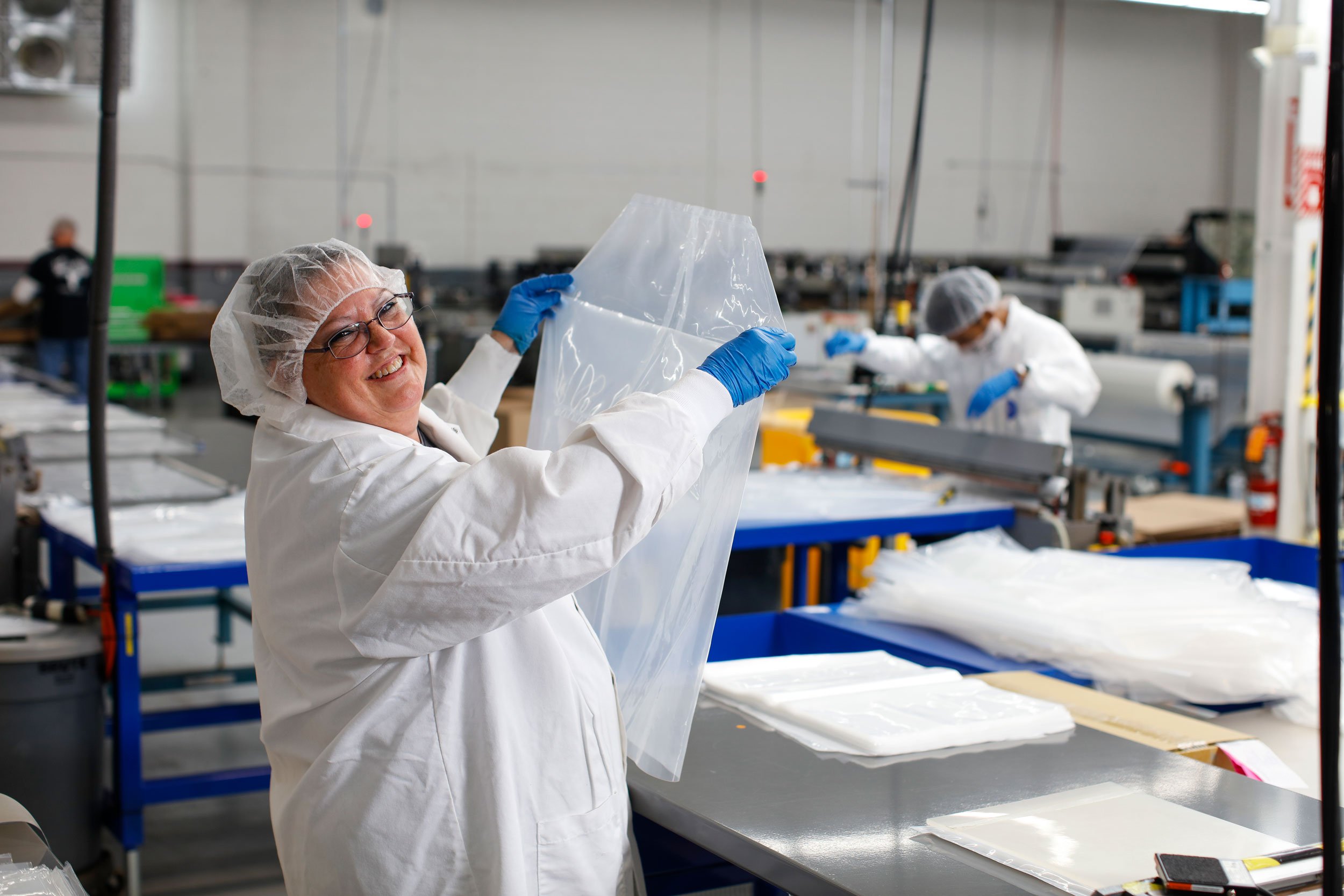
SQF Zone
Safe Quality Food Certified
We are certified in SQF Food Safety Code for Food Packaging, Edition 9, a comprehensive global food safety program.
Our SQF area is equipped to manufacture flexible packaging products that will contain food items and liquids for retail and institutional use, and our employees are trained to live the culture of food safety in all areas of our plant, insuring a safe and clean manufacturing environment.
Frequently Made Products
Stand up pouches with molded fitments for sauces, drink mixes, and more.
Round bottom drum liners with molded fitments and easy tear strips for concentrated ice cream flavoring.
Flat pouches with contour-shaped heat seals and flange fitments installed in-line for powdered eggs.
Flat bags for secondary food packaging.
…and many more!
SQF Equipment & Machinery
Automatic Pouch Making Equipment
Fitment Installation Equipment
Round Bottom Sealing Equipment
Round Bottom Die Cutting Equipment
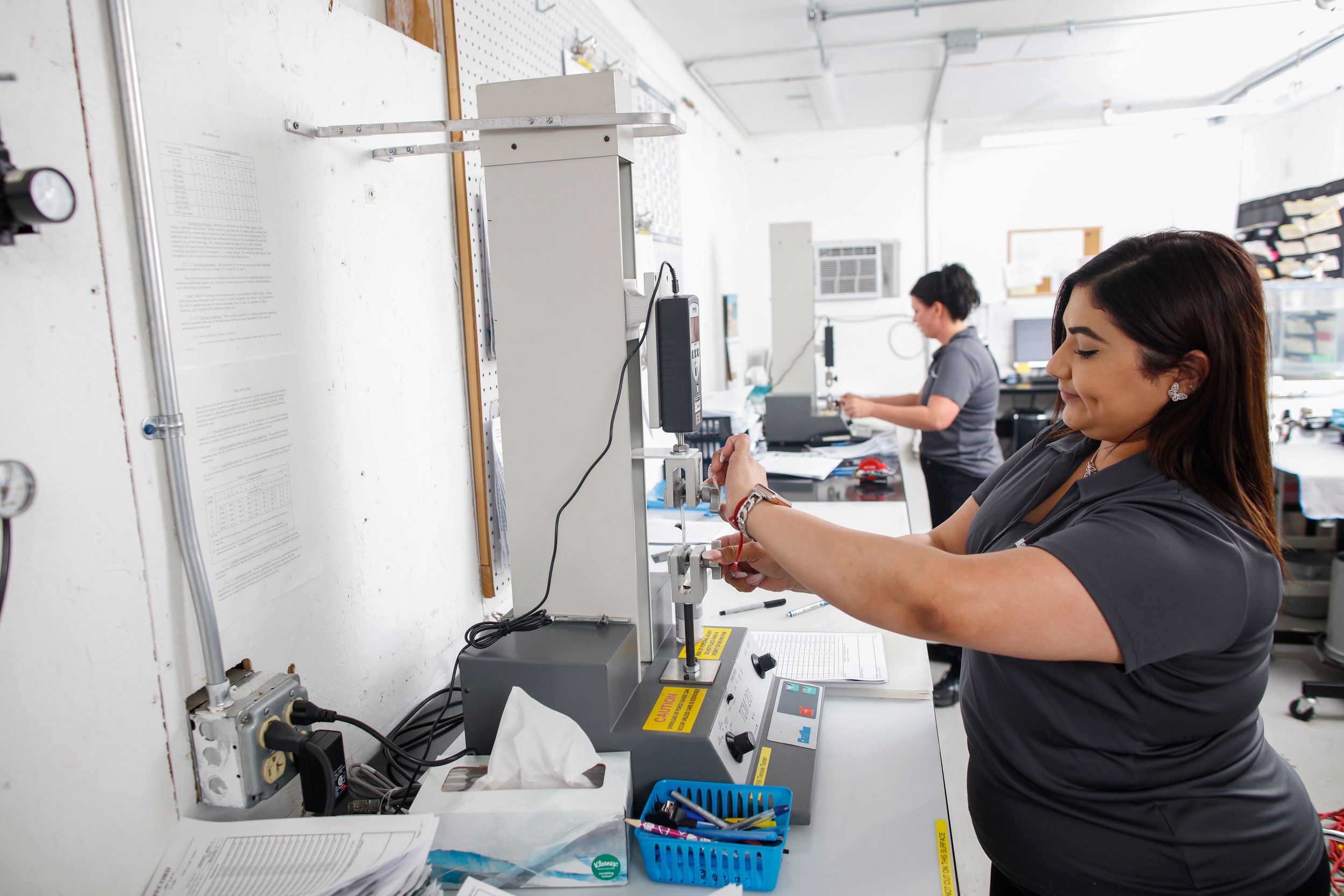
Quality Lab
Quality Assurance
Our quality management system is based on MIL-STD-1916 and includes third-party audited GMP & SQF protocols. All of our made-to-order products receive quality inspections and instrument testing. Our lab houses numerous testing instruments and methods for data entry.
Our quality control team moves about the building constantly during the day, performing checks and tests to ensure all quality standards are met. Additional testing, like drop testing or boil testing, are available upon request.
Our Testing Instruments
Burst strength testing equipment
Tensile testing equipment
Leak/pressure decay testing equipment
Vacuum Chamber (immersion) testing equipment
Mil-Spec hang test equipment
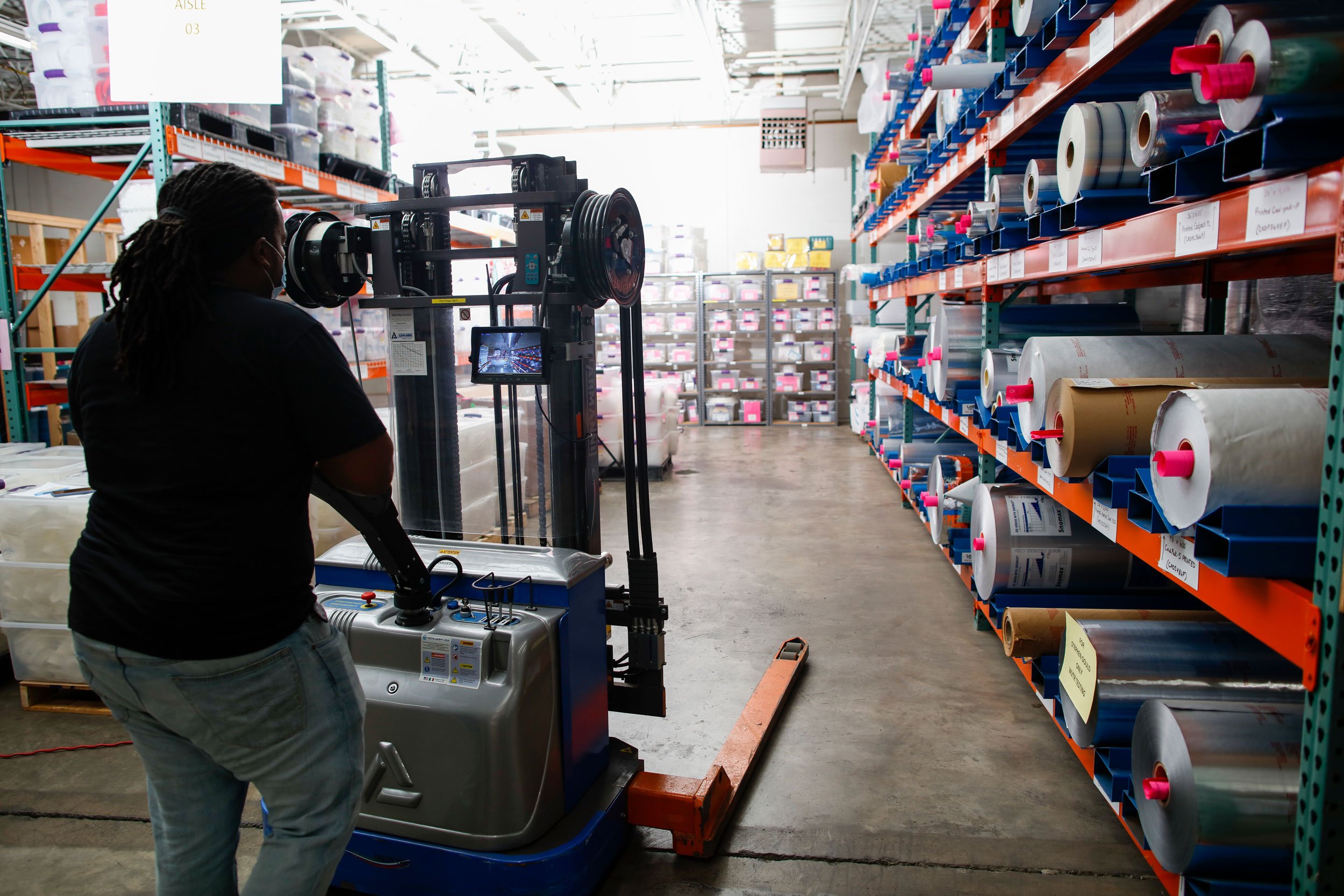
Warehouse
Safe Storage
Separate from our shipping department, our warehouse stores raw materials, and components.
In order to maintain organization, efficiency, and quality, access to the warehouse is limited to authorized personnel only. We use a picklist system to notify handlers what materials are required, which they then select and deliver to designated staging areas on the production floor.
Our Procedures
All materials are stored 18” from perimeter walls, and ample pest mitigation measures are in place and monitored regularly. Raw roll goods are stored in pallet racking as pallet loads, and materials returned from production are placed in rack-mounted metal nests for individual rolls accessed by our roll picker and up-ender. Component parts like valves and molded fitments are weight counted upon receipt and transferred into plastic bins for rack storage.
All warehouse staff members follow GMP & SQF guidelines and codes, as well as our SOP’s for carrier vehicle inspection, incoming materials staging, incoming inspection, and subsequent material tagging and movement to designated storage locations. All materials handling equipment is routinely maintained to promote safe and efficient operation.
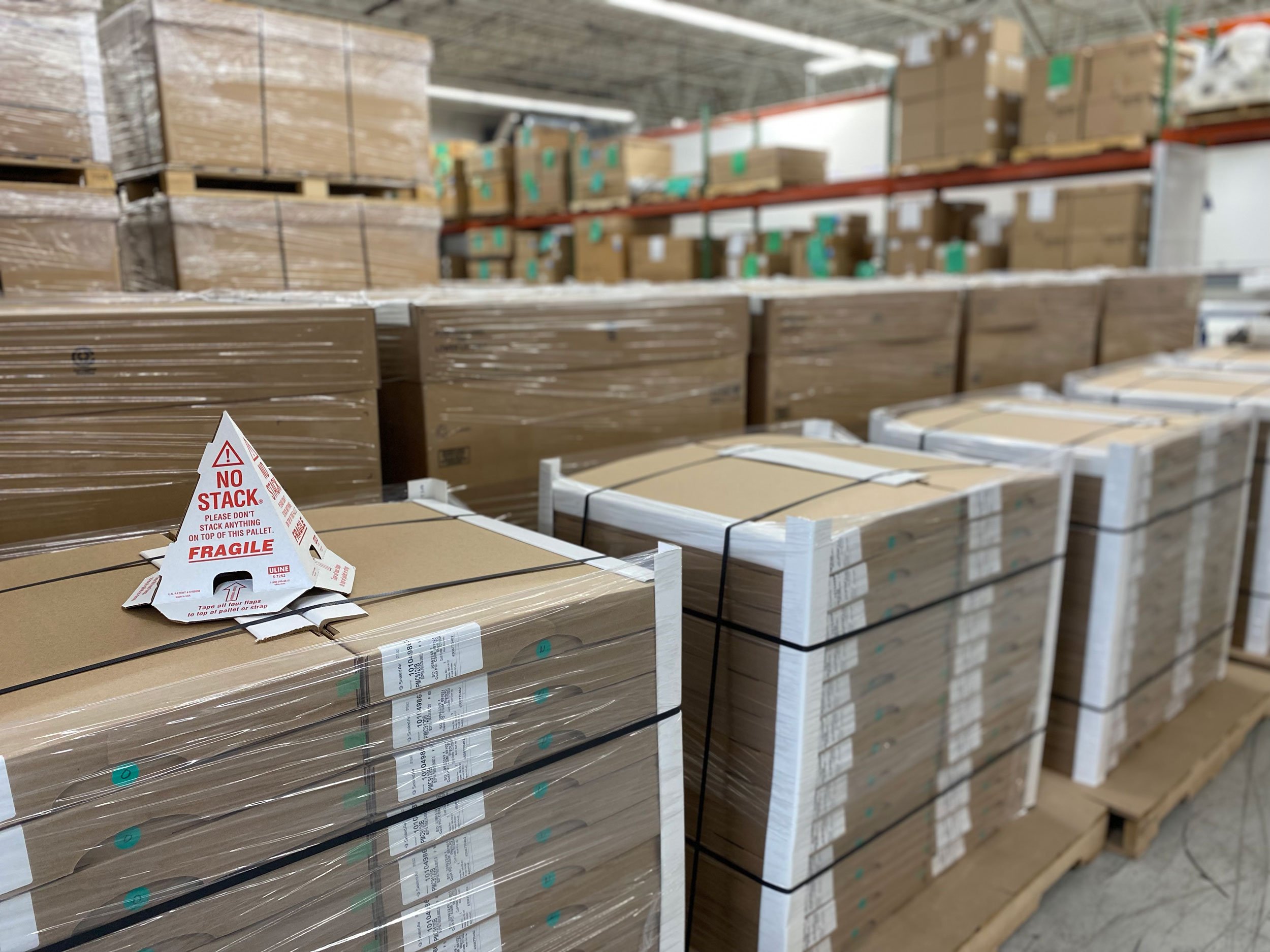
Shipping
Outgoing Finished Product
We are a make-and-ship facility! Customer orders are processed daily in accordance with our standard operating procedures. Once the product is inspected, accepted, and released for shipment it moves to our shipping department, where nothing but finished product and palletization supplies are kept.
Packaging for Our Packaging
Each pallet load is prepped to withstand the rigors of transport using the appropriate packaging materials, pallets, banding, stretch wraps, corner boards, warning placards, and more.
Whether shipments are local or international, our packing process ensures that goods arrive in the same condition they left our facility in.
We inspect trucks prior to loading and photograph every load before the truck departs.